CAPA Process with Example
CAPA Process | Examples
Hi readers, here we are going to discuss the details of the CAPA Process and the ISO standard requirement of concept capa and also describe here with definition and comparison with the new ISO 9001:2015 and IATF 16949:2016 Standard.. as we know the capa word is common in the industry and used for improvement purposes.
Definition of CAPA:
The full Form of CAPA is Corrective Action and Preventive Action. Action to eliminate the root cause of Non-conformity is called Corrective Action. Preventive action is the action to eliminate the potential cause of non-conformity.
Download the Correction and Corrective Action Format/Template.
Concept of CAPA Process in ISO 9001:2015:
According to the new standard ISO 9001:2015, there is no separate clause or sub-clause of preventive action. So now in ISO 9001:2015, preventive action is expressed through the use of risk-based thinking.
CAPA is the combination of two major parts one is Preventive action in the form of Risk, a mitigation plan, and current controls. And another is Corrective Action which has a separate main clause in ISO 9001:2015 Standard in Clause no 10.2.
The main clause 10.2[
Non-conformity and corrective action] has described as
-The organization shall react to non-conformity and will take action to control and correct it.
It means basically asking for the action plan to element the root cause of non-conformity and evaluation of consequence and effectiveness of action and also asking for updating the risk and opportunity.
In the sense of CAPA in ISO 9001:2015 we have to retain documented information as evidence of [1] the Nature of non-conformity and subsequent action taken [2] Results of corrective action [3] Risk Register [4] Current control[5] Mitigation plan of significant risk.
Download the Correction and Corrective Action Format/Template.
Download the CAPA Format/Template.
Similarly Concept of the CAPA Process in IATF 16949:
The concept of CAPA w.r.t IATF 16949 is the combination of ISO 9001:2015 requirements along with the supplemental requirements of IATF 16949 as [1]Problem-solving [2] Error-Proofing [3] warranty management system [4] customer complaint and field failure test analysis.
Let us understand the supplemental requirements very well. In the section on Problem-solving, Correction, corrective action, containment action, root cause analysis, and effectiveness of corrective action need to be formulated. And also asking to update your PFMEA, DFMEA, and Control plan [if required]. And also similarly asking about the correction, corrective action, and effectiveness of action taken on warranty products, customer complaints, and field failure.
Let us take an example here to explain details about the Correction and corrective action:
Say, for example, Customers found damaged products at their end.
So here on the basis of the above complaint, OEM-Automotive Company may ask for 8D. Similarly for this problem, other companies can ask for a correction and corrective action plan. so first of all we will talk about correction, corrective action, containment action, and then document updation.
Containment/Correction Action: Immediately all products should be rechecked at the Dispatch Area before supply to the
Corrective action: Here we need to identify the Root cause of Non-conformity by why-why analysis
Why- 1-Why Damage the product at the customer end?
Ans.- Due to the loose Packaging.
Why-1-Why Loose Packaging?
Ans.- Due to missing out of buffer element
Why –Why missed out of the buffer element?
Ans.- There was not 100% visual inspection to identify such a problem.
Action Plan: 100% Visual inspection will be executed before final packaging.
Document Updation: Control plan, PFMEA.
With the help of the CAPA (Corrective Action & Preventive Action) process, you can improve your process.
More on TECHIEQUALITY

Swot Analysis of Marketing Operation

Repeatability vs Reproducibility | Discussion of Key difference.

Verification vs Validation | What is difference between verification and validation?

5’S Concept | What are 5’S?

Rework vs Repair |IATF Requirement for Control of Reworked/ Repaired Product

Corrective Action vs Preventive Action

Kaizen vs Innovation | Key Differences between Kaizen and Innovation

How to plot the Run Chart in Excel | Run Chart Excel Template:

How to plot the Run Chart in Minitab

How to calculate Cp and Cpk? | Practical Case Study | Process Capability Example
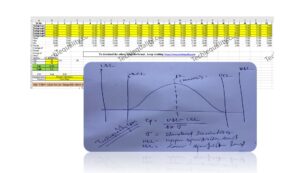
Process Capability Analysis | Cp & Cpk Calculation Excel Sheet with Example

How to do Capability Analysis by Minitab 18? | Minitab Process Capability Tutorial
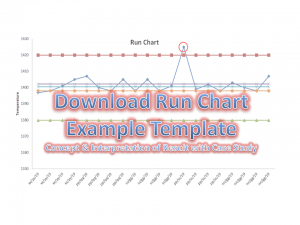
Run Chart Example | Concept & Interpretation of Result with Case Study | Industrial Example:
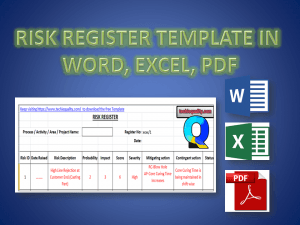
Risk Register | Download Risk Register Template:
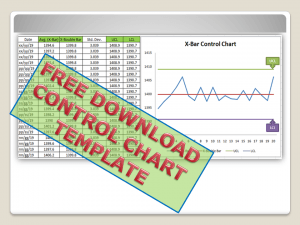
Control Chart Excel Template | How to Plot Control Chart in Excel | Download Template

8D Report Example | Download Case Study Report:

Control Chart in Minitab | How to plot a Control Chart in Minitab
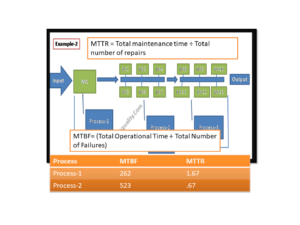
MTBF and MTTR Template, Format, Calculation | Manufacturing Example
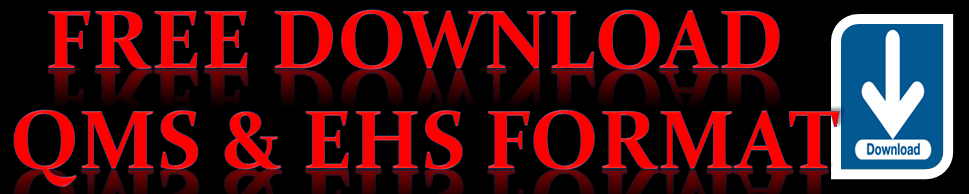
Thank you for reading ……….. Keep Visiting Techiequality
Popular Post: