The Process Approach to QMS (ISO 9001, IATF 16949):
Process Approach:
Hello readers! Today we will discuss the process approach. Why QMS standard (ISO 9001, IATF 16949) promotes the adoption of a process approach when developing, implementing, and improving the effectiveness of a quality management system, to enhance customer satisfaction by meeting customer requirements. As per ISO definition process approach is; Understanding and managing interrelated processes as a system contributes to the organization’s effectiveness and efficiency in achieving its intended results. This approach enables the organization to control the interrelationships and interdependencies among the processes of the system so that the overall performance of the organization can be enhanced.
DOWNLOAD-7QC Tools and SPC Templates.
You could also like to read our below articles;
7 principles of QMS | Quality Management Principles
Risk identification tools and techniques |Download Format
SPC Format |DOWNLOAD Excel Template of SPC Study
why-why analysis methodology | 5-why analysis step by step guide
The Decision of process capability analysis |Download Format
UNDERSTANDING OF PROCESS APPROACH WITH EXAMPLE:
As we know organizations have several departments for executing a certain activity. And for multiple processes, it’s difficult to understand the process interaction and department involvement. So the process approach will help you to meet the intended result of QMS and Customer requirements. Every process follows the PDCA cycle to complete the activities as plan-do-check-act. For completing the cycle of PDCA, the individual department will be involved in the appropriate phase. The Schematic diagram of multiple processes is given below.
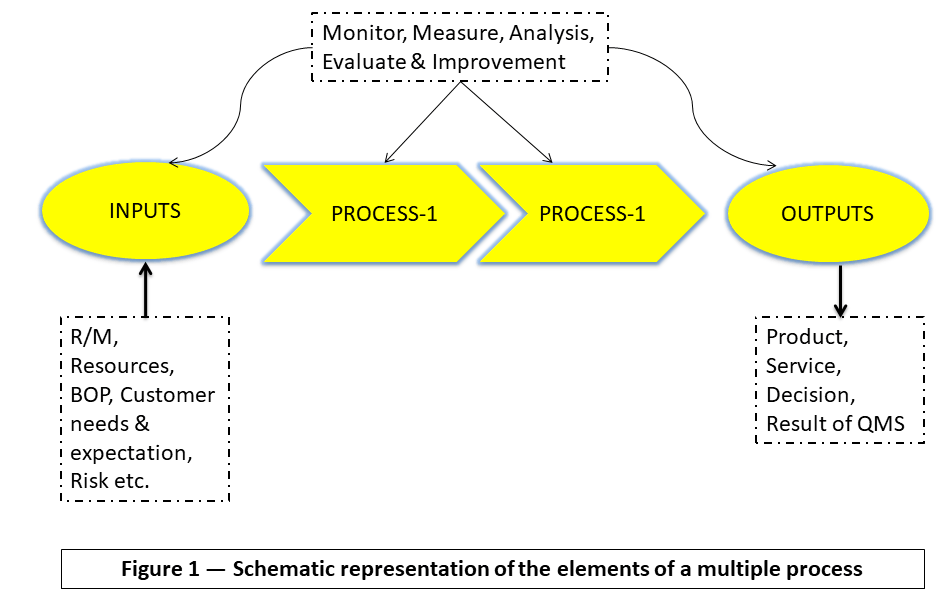
The process approach is one of the Principles of QMS.
How a company correlates its activity after getting orders from customers:
Basically, the customer intimates the order to the customer representative (marketing) and then the organization executes the job activities according to their process approach. Subsequent to the customer requirement, the PPC department prepares the monthly/shift-wise plan and accordingly informs to support department for readiness and prompt supply of input requirements. Then the process manager arranges the process accordingly to execute the process and simultaneously QC team monitors the process and product characteristics to confirm the product and allow passing the next operation and doing so the product is made and supplied to the customer with the fulfillment of their requirement. I hope you got a complete idea of how the process and several departments have interacted with each other to complete the jobs. So actually this is called the process approach.
Similar Topics:
Error Proofing Understanding & Implementation of IATF 16949 Clauses 10.2.4.
Rework vs Repair |IATF Requirement for Control of Reworked/ Repaired Product
Risk Register | Download Risk Register Template.
Risk Management Process | Risk related to IATF 16949, ISO 9001, ISO 14001, and ISO 45001.
8D Report Example | Download Case Study Report.
Thank you for reading…keeps visiting Techiequality.Com
Popular Post: