Plan Do Check Act Cycle | PDCA Cycle Manufacturing Example | Implementation
Plan Do Check Act Cycle | PDCA Cycle Manufacturing Example | Implementation:
Hi readers! Here, we will discuss the details on PDCA cycle (Plan Do Check Act Cycle) with the Industrial/ Manufacturing example. The PDCA Cycle is the most popular cycle/ method used in industry/ organization for continuous/continual improvement and process improvement and problem solving. The PDCA cycle consists of four phases i.e. [1] Plan, [2] Do, [3] Check, & [4] Act. The Plan-Do-Check-Act Cycle is also called as Deming Cycle/Wheel, PDSA Cycle (Plan-Do-Study-Act), or Plan-Do-Check-Adjust Cycle.
Plan Do Check Act Cycle / PDCA Cycle / Deming Cycle:
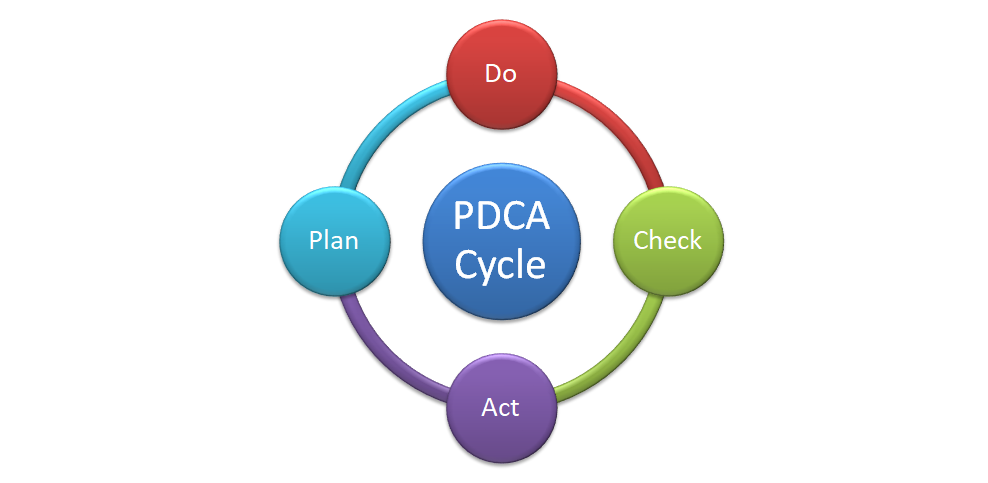
Basically, the PDCA (Plan-Do-Check-Act) cycle is used for continual/ continuous improvement. If you find any problem in the production process or would like to improve the production process then you can easily apply this management approach. But you can apply this PDCA cycle to any type of improvement project/ objectives. It is not only used for Process improvement but also used for Problem-solving. The details of individual stages /phases are described in below.
Plan: To develop the Potential solutions.
Do: To execute the Plan.
Check: To Review, verify, inspect, evaluate, analyze the data, and compare the results (Before and after) w.r.t Objectives that the plan/solution is satisfactory or not.
Act: If the solution is satisfactory then implement it. If it is not satisfactory then take the containment action and repeat the Cycle.
How to Implement PDCA Cycle in the Manufacturing Industry for Continuous/ Continual Improvement:
I am so excited to share my own experience. I have implemented so many improvement projects through the PDCA Cycle, but here I am going to share only manufacturing process improvement-related examples.
When we had prepared the monthly quality report of the manufacturing process, we got that the shrinkage problem was a vital problem and almost contribute the 30% among the entire problem and on the basis of the report we have decided to improve the process and to reduce at least shrinkage defect from 30% to 5%. Accordingly, objective has been taken and followed the PDCA cycle to resolve it and to improve the manufacturing process.
PLAN:
Before applying the method, we have formed a Team and described the problem, took the objective, and prepared the plan, which is described as below.
Step-by-step method that we have followed to prepare the Plan:
1] To Form a Team.
2] To Take an Objective.
3] To Prepare the Roadmap /Activities flow chart.
Team Formation:
Name of Project Leader: Mr. S |
Name of Team members: |
Mr. G |
Mr. P |
Mr. N |
Note: During the team formation, you may consider the members from different and different sections, that are directly associated with your process activity. Because you can easily manage your activities.
Now, the next step is to take an Objective.
Objective: To reduce the Shrinkage defect contribution from 30% to 5% within 3 months.
According to the above objective we have prepared the Plan. And details of the plan are described below.
Activities | Responsibility | Time-Line |
Data Collection | Mr. G | Within 7 days from the starting date of assignment. |
Cause and Effect diagram Preparation | Mr. G & Mr. P | (Within 9 days from the starting date of assignment) |
Identify the significant causes | Mr. G & Mr. P | Within 15 days from the starting date of assignment. |
Why-Why Analysis | Mr. G, Mr. P & Mr. N | Within 20 days from the starting date of assignment. |
Identify the Root Cause | Mr. G, Mr. P & Mr. N | Within 21 days from the starting date of assignment. |
Corrective Action plan | Mr. G, Mr. P & Mr. N | Within 25 days from the starting date of assignment. |
Preventive Action plan | Mr. G, Mr. P & Mr. N | Within 25 days from the starting date of assignment. |
Trial implementation | Mr. G, Mr. P, Mr. N & Mr. S | Within 75 days from the starting date of assignment. |
Comparative study w.r.t Objectives | Mr. G, Mr. P, Mr. N & Mr. S | Within 90 days from the starting date of assignment. |
[Table-A, Activities Plan Flow, Plan do check act example /PDCA Example]
Note: The above activities may change according to the nature of the improvement project. Or whatever objective you have taken. The Aforesaid plan template is only for your reference.
In this way, you may prepare the Plan. Now, we have to move on to the next phase of the PDCA Cycle i.e. “DO”
DO:
In the “DO” phase, you are supposed to implement the Plan that you have prepared in Plan phase. As you can see that we have already prepared the Activity plan and represented in Table-A, and the same implemented.
According to the management approval, we have manufactured the 5-samples as trial implementation. And next activity was done in the “Check” phase.
CHECK:
After trial implementation, whatever data we have collected, just we analyzed all the things, did the gap analysis and we compared the results w.r.t Objectives. And recorded the significant points & collected the feedback as well.
As you know that this phase is important so you have to study and analyze all the things. Similarly, we have compared the results w.r.t Objectives and found the below result.
Before Data (old methods/ before implementation of improvement plan)
Shrinkage defect contribution = 30%.
After Data (New methods/ after implementation of improvement plan)
Shrinkage defect contribution = 5%.
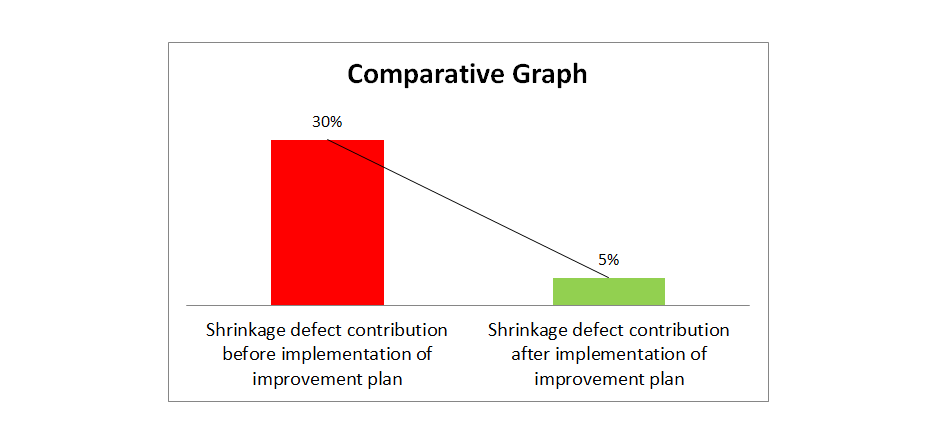
Conclusion: We have found that the improvement plan is effective and satisfactory.
We have achieved the Objective’s target value. So we have informed to top management about the action plan results to act on it.
ACT:
In the above example, we have found that the solution/improvement plan is satisfactory. So we have finally implemented the new action plan and standardized it.
If applicable then do the horizontal deployment also.
FAQ:
What do you need to do if your objective will not be achieved?
Ans.: In the “Check” phase when you will find that your objective is not achieved, then you have to take the containment action and you have to repeat the PDCA cycle until resolve the problem or improve the process.
What does PDCA stand for?
Ans.: The full form of PDCA is Plan-Do-Check-Act, and also it is called as Plan do study act, plan do check adjust, Deming Cycle, and Shewhart Cycle.
How does PDCA Improve Quality?
Ans.: Go through the above manufacturing example (Shrinkage Issue), step by Step-by-step phases are mentioned there.
How do you use the PDCA cycle?
Ans.: As you know the PDCA cycle is generally used for continuous /continual improvement. To do so, you have to follow the cycle principles.
1] To form a team
2] To take an objectives
3] To prepare the roadmap/ activities plan
4] Step by step implement the plan.
5] Study the data and compare the results with respect to the objective.
6] Implement the solution (Final implementation); if the result is coming satisfactory otherwise take a containment action and repeat the PDCA cycle again until achieve the Objective’s target value.
Free Templates / Formats of QM: we have published some free templates or formats related to Quality Management with manufacturing / industrial practical examples for better understanding and learning. if you have not yet read these free template articles/posts then, you could visit our “Template/Format” section. Thanks for reading…keep visiting techiequality.com
Useful Post:
Types of Productivity with Example |Productivity Formula |Calculation
How to Calculate Correlation Coefficient (r) |Correlation Coefficient Formula
Correlation Analysis Example and Interpretation of Result
Correlation Analysis in Minitab |Step by step guide with example
More on TECHIEQUALITY