How to enhance production in manufacturing unit?
How to enhance production in manufacturing unit?
Hello readers! Today we will discuss on How to enhance production in manufacturing unit. So you know that enhancing the production quantity with the same capacity is a big challenge in the manufacturing industry. Changing the mindset of manpower (operators, unions, staff, etc.) is another challenge. So here we will discuss on same points to overcome such type of issue and will give you some solutions that you need to follow some below steps for enhancing the production quantity. Many organizations are giving more focus on cost reduction in several ways. As you know that if organisations will succeed in the below parameters then definitely they shall enhance the turnover.
- To Reduce the COPQ.
- Eliminate the wastage.
- Comprehensive PPC.
In a wide range, there are so many parameters that we need to give more focus to improve them step by step. Some are mentioned in below figure;
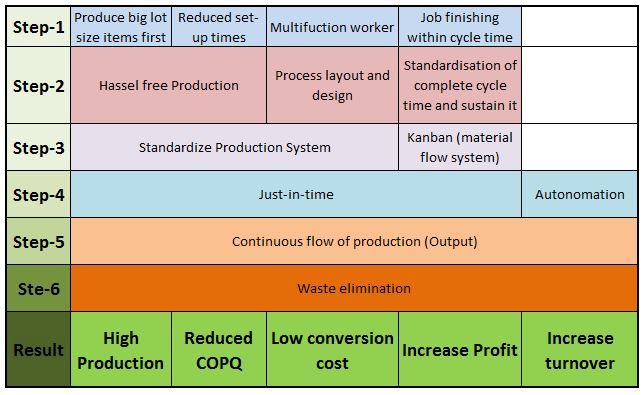
Before we discuss step by step, kindly have a quick look at the above figure first. Many organizations skip the little things or do not consider them during production planning due to some unavoidable circumstance. But later on, they face many problems at the in-process, customer end, and business planning levels.
Details on How to enhance production in manufacturing unit:
Frequently changing of production tooling may take more set-up time which can reduce the quantity needed to be produced. Consider big lot-size items first and reduce the tool set-up time by introducing SMDC methodology, and automatic tooling handling, by reducing the tool repairing time, by enhancing the skill level of personnel, by introducing the tooling management system. etc.
The multifunction worker can reduce the job finishing cycle time by doing multiple jobs at a time in a standardized machine layout. Many automobile manufacturing industries have installed the machine in a ‘U-layout’ at the assembly process. This layout is the most popular one in the automobile manufacturing industry which can reduce the operation cycle time and manpower as well.
After completion of the above job, now it’s time to think about the smooth movement of incoming material to the operation process, quality control at place and just-in time. For doing so KANBAN methodology is the older one but is more effective and helpful for the smooth movement of material for pre and post-operation. And for quality control, many organization transferred their traditional manual process to Autonomation. In this platform, organizations are installing the Andon system, Poka-yoke (Error proofing), Yo-i-don (Ready, set, go). Same you can introduce in your manufacturing process.
For just-in-time, an organization has to work hard at their supplier end as well as their own process. Just-in-time’s primary focus is zero inventories. If you will succeed in implementing the Jus-in-time concept at your and the vendor’s end then the organization can reduce the wastage. There are so many initiatives available to eliminate wastage like Lean manufacturing, lean design, Lean six-sigma, Quality circle concept, and kaizen, TPM (OEE improvement and loss reduction), etc.
Useful articles (Knowledge Factory):
Quality at the source | Steps to Implement It.
Jidoka Autonomation, Bakayoke & Yo-I-don |Concept in TPS.
Pull Production System | Concept.
Toyota Production System History
Toyota Production System Tools & Technique
Tools, template and Format-Download.
Thank you for reading…keep visiting Techiequality.Com
Popular Post: