Jidoka Autonomation, Bakayoke & Yo-I-don |Concept in TPS
Jidoka Autonomation, Bakayoke & Yo-I-don |Concept in TPS
Hello Reader! Here we will describe three important elements of TPS (Toyota Production System) are Autonomation (Jidoka), Bakayoke & Yo-i-don. These three elements are very useful and frequently used in manufacturing units to reduce the number of defectives products and improve the quality of the process.
Read more…TPS, TPS History, Pull Production System.
(Jidoka) Autonomation:
Autonomation is a word coined by Toyota that means Autonomous defect control. Jidoka allows the operation to have a built-in quality at each work step so that the workforce (operators) does not have to watch the operation or machine to control the process defect.
Illustration:
Autonomation (Jidoka) doesn’t pass the defect to nest operation, doesn’t make defects, and doesn’t accept defects. The Must-probably production system is controlled by the just-in-time system but if there is an existing of process defect the autonomation system will help you to control the process defect control for an automatic process, if it’s a manual process then we have to implement the Bakayoke system which is the older name of Poka-yoke (Error proofing).
Sometimes in a fully manual process where Bakayoke is not possible to implement, normally a red colour stop button is used for any defects detected during operation. The line problem is then fixed up before work is resumed. Andon light system is generally used in the Jidoka system.
Andon light system:
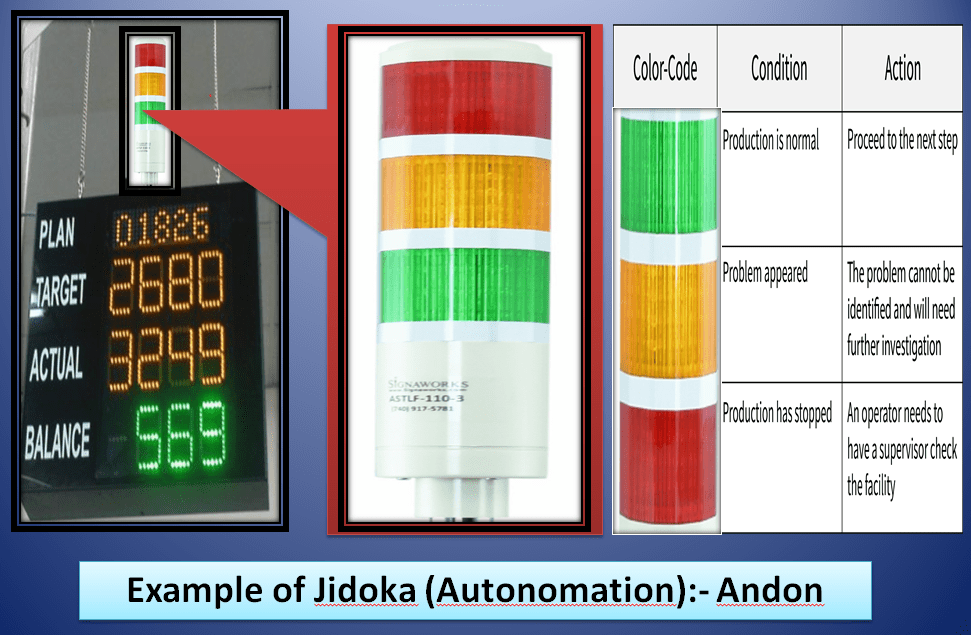
Details: Generally andon light system having three different colors. Which indicates some meaning to take action i.e.
Colour Code | Condition | Action |
Green | Normal Operation | Move on to the next operation |
Yellow | Problem Appeared | Fix up the problem |
Red | Production or M/C stopped | The Problem needs to be identified and to be fixed up |
This is one of the best tools which is frequently used in the manufacturing industry. But in a fully automation factory, machines or operations can be controlled through a wireless, or wifi connection to control the process or machine defect smartly and you can resolve the problem very promptly.
Yo-I-Don system:
It means Ready, set, go. This system involves teamwork between adjacent operations to ensure that work at the station is balanced. After completion of operation at each work station, all operators need to press the special button if any station sees a red light, which means it indicates delays and the entire line stops until all red lights are off. When this happens, workers nearby help each other to complete the work.
After completion of operation at each work station, all operators need to press the special button if any station has seen the red light, which means it indicates delays and the entire line stops until all red lights are off. When this happens, workers nearby help each other to complete the work.
After completion of operation at each work station all operators need to press the special button if any station has seen the red light, which means it indicates delays and the entire line stops until all red lights are off. When this happens, workers nearby help each other to complete the work.
Benefits of Autonomation:
- Reduces the number of defective product
- To increase the productivity
- Improve the process quality
- Empowers peoples
- Enable separation of interested parties’ work and machine.
- Prevent defective (Before delivering to the next workstation.
- Man-power saving
Useful Articles:
Histogram Template with example | Download
Verification vs Validation | What is the difference between verification and validation?
Kaizen vs Innovation | Key Differences between Kaizen and Innovation
Thank you for reading…Keep visiting Techiequality.Com
Popular Post: