Error Proofing Understanding & Implementation of IATF 16949 Clauses 10.2.4
Error Proofing Understanding & Implementation of IATF 16949 Clauses 10.2.4
Error Proofing/ Poka-Yoke is a Japanese word that means ‘mistake-proofing’. Its main goal is to eliminate Process defects by preventing, correcting, or drawing attention to human errors. This concept was implemented during the TPS (Toyota Production System). The actual term used in TPS is Bakayoke but in later it was changed to Poka-Yoke.
DOWNLOAD the Risk identification Format/ Template and its Procedure as per IATF 16949 & ISO 9001 with example.
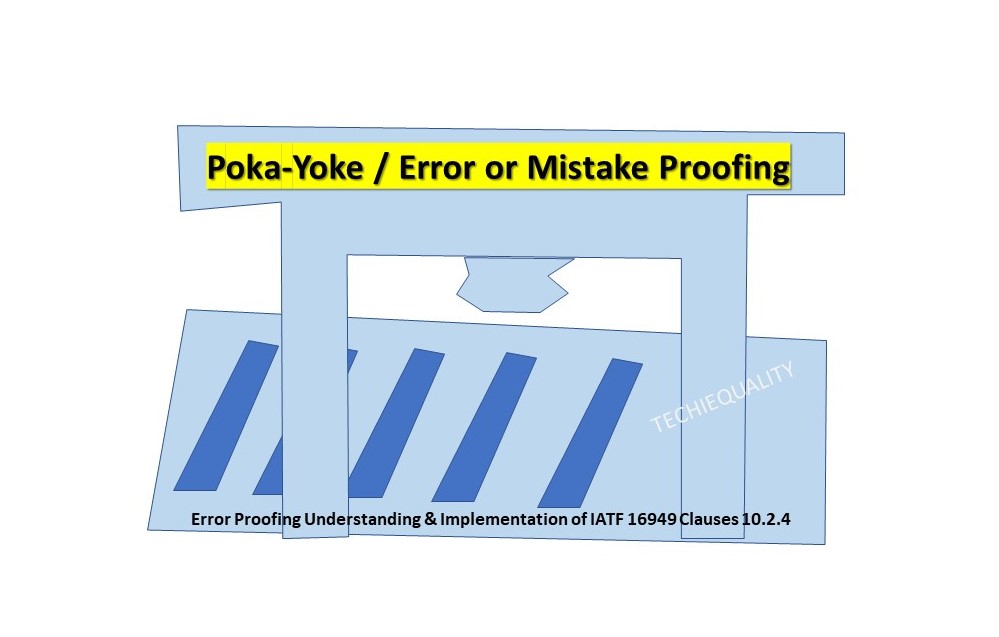
In the 1960s, Shigeo Shingo had applied the term poka-yoke in the industry to prevent human error. The error-proofing is also called as poka-yoke, mistake-proofing, and bakayoke. But the term used in IATF 16949 standards is Error-Proofing in clause no. 10.2.4. Detail has described the standard requirement in below. purpose of poka-yokel the good product to subsequent process and block the defective product without any human interference.
How to select and install Error Proofing devices :
- Study the process.
- Identify the “Q” component and decision-making points
- You can make a special automation device w.r.t your process and machine layout.
- Install the poke-yoke or automatic defect control devices.
Benefits:
- Less time spent on On-Job training.
- Elimination of manual defect control.
- The unburdening of the QA person.
- Enhance customer satisfaction.
- 100% defect control.
- Eliminating defects before they occur.
Understanding and Implementation of requirements of Error-Proofing / Poka-Yoke / Mistake-Proofing according to IATF 16949 (Clause no 10.2.4):
- An organization needs to prepare a Procedure to determine the use of mistake-proofing And the same Poka-yoke methods are supposed to address in FMEA.
- Now test frequency shall be defined and the same link to be given in the Control Plan or QAP (Quality Assurance Plan).
Record s of such tests of poka-yoke need to be retained by the organization.- If any poka-yoke fails to work, then the organization should have a reaction plan for the failure of Error-proofing/ Poka-yoke.
To fulfill the mandatory requirements of clause 10.2.4 (IATF 16949), we have to implement the above four points in practice.
How to Identify Error-proofing opportunities in a process or operation?
Now, we are going to discuss a very interesting topic that is more practical in manufacturing, as we know that error proofing is also called Poka-yoke or mistake proofing which is used to prevent the mistake during a process or operation. Below is the step-by-step process to identify the mistake-proofing opportunities in an operation or process.
Understand the Process or Operation:
First of all, you have to understand the entire process or operation before going to identify the mistake-proofing opportunities. For better understanding try to involve and talk to the operators, employees, supervisors, etc. of that process and review the PFD and documentation.
Identify the potential failures.
Just interact with shop floor people and try to go through the Gemba audit to identify the points in the operation where mistakes are likely to occur. And note down these points for further analysis.
Analyze the opportunity points
Review the opportunity points and discuss with the engineering teams to find out the mistake-proofing resolution. For example, camera installation, device, automation, sense installation, gauge, etc for pokayoke the operation or measurement.
- Evaluate the feasibility and cost of the error-proofing solution.
- Pilot Test: Try to conduct the pilot test of poka-yoke measurement before implementation in the entire process or operation.
- Full-phase implementation of poka-yoke measurement or device after getting the desired result from pilot testing.
- Document the error proofing and establish the periodic testing
- Provide training to operators related to error-proofing usages and handling and if possible, you can display the feature points on the shop floor for quick reference.
Useful Articles:
Pareto Chart Example of Manufacturing Units
Verification vs Validation | What is the difference between verification and validation?
Thank you for Reading… Keep visiting Techiequality.Com
If you require any further information, feel free to contact us.
Popular Post: