AIAG VDA FMEA Key Changes | Overview | 7 Step FMEA |PFMEA |1st Edition 2019 | Training
AIAG VDA FMEA Key Changes | Overview | 7 Step FMEA |PFMEA |1st Edition 2019 | Training
The AIAG VDA FMEA 1st edition handbook has been released first time jointly by AIAG (Automotive Industry Action Group) & VDA (Verband der Automobilindustrie) in 2019. Basically, FMEA is a core tool that is used to identify the potential failure modes of process and product & their cause and effects. Mainly FMEA is three types i.e. [1] PFMEA (Process failure mode and effect analysis), [2] DFMEA (Design failure mode and effect analysis), [3] MSR-FMEA. In this post, we will cover the PFMEA with a manufacturing example.
DOWNLOAD-PDF files of AIAG-VDA FMEA key changes.
If your organization is manufacturing Automotive /Automobile parts/items/products or IATF 16949 certified companies then, you are compulsory to identify the process/ product /design related failures /risks in the FMEA worksheet. It means you have to prepare and implement the FMEA in your organization as a live document. If a customer mentions in their CSR (Customer Specific Requirement) for FMEA requirement then, it’s mandatory for their supplier to fulfil the FMEA requirement, but it does not matter whether your organization is IATF-16949 certified or not. So it’s more important to understand the complete requirements of FMEA before its application in industries. In standard IATF-16949, the application of FMEA is clearly mentioned in several clauses. Now we are going to explain each and every clause of IATF-16949 those are relevant to the FMEA application.
What are the requirements of IATF 16949 for FMEA application?
There are almost 12 sub-clauses in the IATF-16949 standard, where the application and implementation of FMEA are widely explained in the IATF standard. These clauses’s requirements as explained below;
IATF-16949 Clauses /Sub-clauses No: 4.4.1.2: Special approval of PFMEA and DFMEA is required.
8.3.2.1 (IATF Sub-clause): During product development, the organization shall develop the DFMEA and require reviewing the product design risk to reduce the potential risks.
8.3.3.3 (IATF Sub-clause): Special characteristics like fit & function, Critical characteristics, significant characteristics, safety characteristics, etc. are need to be included in the FMEA worksheet.
8.3.5.1 (IATF Sub-clause): This sub-clause talks about the design risk analysis. DFMEA is the mandatory requirement for design and development output.
8.3.5.2 (IATF Sub-clause): Manufacturing process-related risks need to be addressed in PFMEA.
8.5.6.1.1 (IATF Sub-clause): Process-related risks need to be addressed in PFMEA due to temporary changes in process controls. If your organization has temporarily changed the existing process controls and using the alternative new control method then, the organization shall include the risks of new process control methods in the PFMEA worksheet.
8.7.1.4 (IATF Sub-clause): The organization shall identify the risks related to the product rework process in FMEA.
8.7.1.5 (IATF Sub-clause): The organization shall identify the risks related to the product repair process in FMEA.
9.1.1.1 (IATF Sub-clause): This clause is about the Implementation of PFMEA.
9.3.2.1 (IATF Sub-clause): Field failure /warranty failure-related risk needs to be addressed in FMEA.
10.2.3 (IATF Sub-clause): As and when problems arise in the process, accordingly review and updation of PFMEA are required.
10.2.4 (IATF Sub-clause): Error proofing details methodology needs to be addressed in PFMEA.
Key Changes of AIAG-VDA PFMEA, 1st edition 2019:
4th edition FMEA (Old version manual) | AIAG-VDA FMEA (New version handbook) |
RPN (Risk priority number) = S x O x D | Action Priority (AP) Table. |
Old Severity, Occurrence & Detection Ratings | Revised Severity, Occurrence & Detection Ratings |
Old worksheet (Format/ Template) | Revised worksheet (Format/ Template) |
PFD was not an integral part | The Process flow diagram is an integral part of the new manual |
Recommended action | Prevention & detection action |
Classification | Special Characteristics |
4M-Men, Machine, Material, and Method approach |
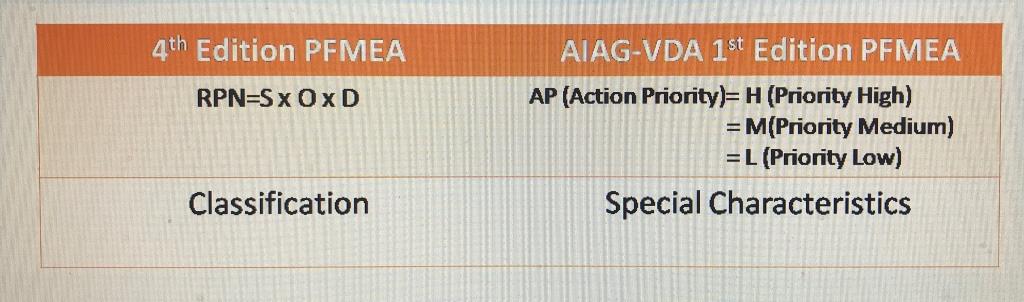
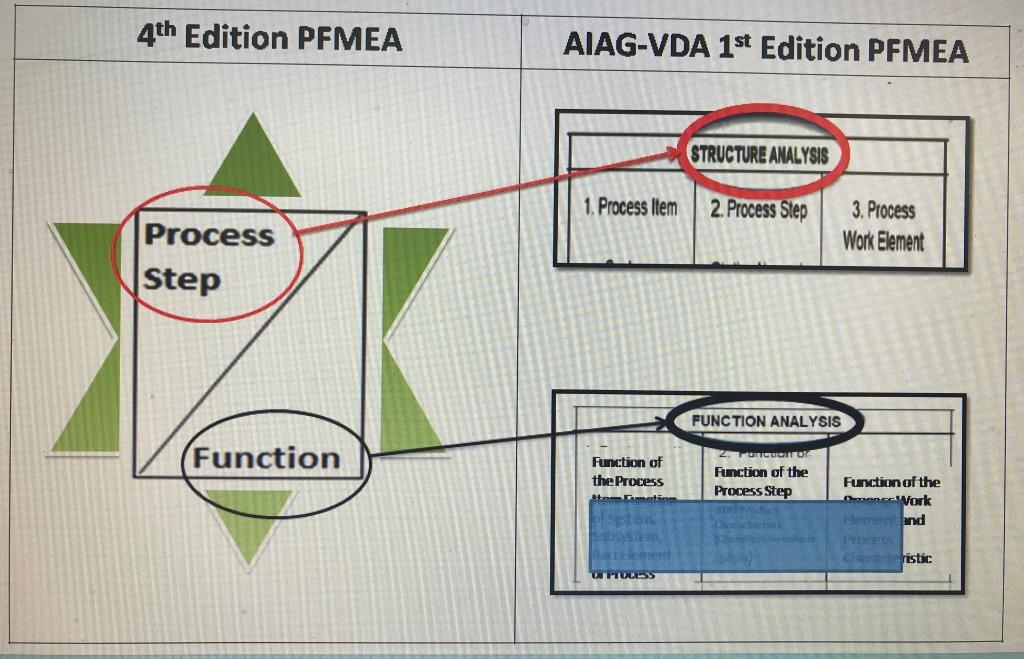
The complete PFMEA worksheet has made considering 7 Steps FMEA approach, i.e. [1] Planning & Preparation, [2] Structure Analysis, [3] Function Analysis, [4] Failure Analysis, [5] Risk Analysis, [6] Optimization and [7] Risk Communication.
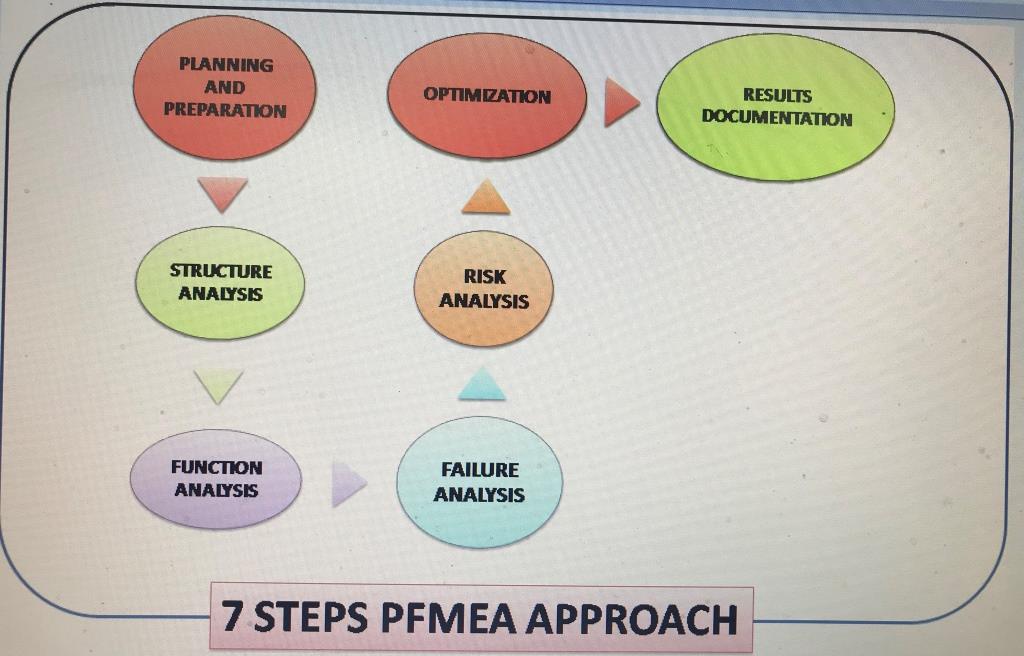
7 Steps PFMEA Approach:
Planning & Preparation:
This is the first step of the FMEA 7-step approach, A Cross-functional team needs to be formed and their roles and responsibilities need to be assigned. In the worksheet, you have to mention those things like Company name, location, PFMEA ID, Confidential Level, etc.
Structure Analysis:
In SA, You have to identify the Process steps i.e. PFD, here you have to identify mainly three things, Process Item, step, and work element (4M).
Function Analysis:
You have to describe the function process item in the next plant process, end-user, and customer, and Simultaneously Process and product characteristics need to be identified.
Failure Analysis:
Here you have to identify the failure effect, mode, and cause.
Risk Analysis:
Current prevention & detection control, AP, SC, etc. need to be addressed.
Optimization:
According to the Level of AP (Action Priority), if required to take the action then, you have to complete the optimization step and again you have to level the PFMEA-AP.
In the previous version, there is a calculation of RPN, but in the new FMEA there is no calculation, just you have to identify the level from the Action Priority Table. Priority High AP level means you must be required to identify appropriate action, Medium priority AP level means you should identify appropriate actions and finally Low priority level (L) means you could identify actions to improve prevention or detection controls.
Result Documentation / Risk Communication:
Now, you have to keep the documents like result communication, CFT meeting report, etc.
7 Steps to Implement the New AIAG-VDA PFMEA in Industry?
In each and every post our authors are trying to share their experience with industrial examples so that the common man can easily understand, learn, and implement it in their workplace. Also, we are always trying to enhance the skill base knowledge of our readers. Anyway, go through the below steps to implement the new PFMEA manual.
Step-1:
To form a CFT team, for example, members should be from different functions like Production, Maintenance, Process quality, product quality, R&D function, etc.
Step-2:
Use the process flow diagram to identify each step of all processes.
Step-3:
Visit the workplace and understand the operational function of each and every step of the process and 4M factors.
Step-4:
Brainstorm the potential failure mode and its effects. accumulate the previous failures from any resources like from shop floor supervisors, operators, from old data, failure due to 4M factors (Man, Machine, Material, Method, etc), and list up the potential effect of failures as well.
Step-5:
To rank the Severity, occurrence, and detection and accordingly choose the level of Action Priority from the AP table.
Step-6:
To address the Current control mechanism in the worksheet.
Step-7:
Take action as per AP level and after implementation of the Action Plan, you have to re-level the PFMEA action priority.
FAQ:
Q1: Shall I need to convert our Approved old PFMEA worksheet to the new one?
A1: Actually it depends upon your customer’s needs and what they want, they need to keep the old approved copy or need the re-approved copy as per the new manual. If your customer asks for a new worksheet as per the 1st edition of AIAG-VDA PFMEA then only you need to change the old one.
Example:
Let’s take an example related to field failure, there is a leakage issue found in the sump chamber, and the same issue was communicated by customers to their supplier to submit the CAPA and updated FMEA. when the supplier investigated the defective product, they found leakage caused due to sand inclusion in the sump base wall. Basically, here, we will focus on how to identify the action priority level of a failure mode. Let you have selected the Severity of FE (Failure effects), Occurrence of FC (Failure cause), and Detection of FC/FM as 9, 2, 1
Effect | S | Prediction of failure cause occurring | O | Ability to detect | D | Action Priority (AP) |
Product or Plant effect very high | 9-10 | Low | 2-3 | Low-Very low | 7-10 | H |
Product or Plant effect very high | 9-10 | Low | 2-3 | Moderate | 5-6 | M |
Product or Plant effect very high | 9-10 | Low | 2-3 | High | 2-4 | L |
Product or Plant effect very high | 9-10 | Low | 2-3 | Very High | 1 | L |
In the above example, the rating of Severity (S) is 9, Occurrence (O) is 2, and Detection (D) is 1. So now, we will match the value in the AP table to find out the AP level. Go through the below picture to know the AP level.
NEW AIAG VDA FMEA AP TABLE EXAMPLE
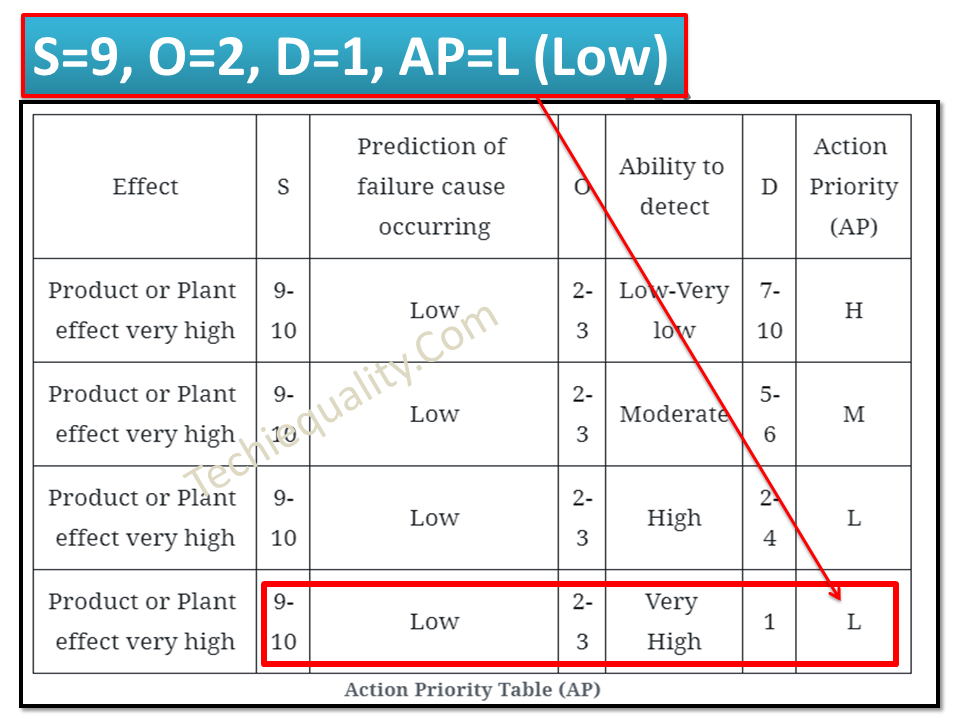
Free Templates / Formats of QM: we have published some free templates or formats related to Quality Management with manufacturing / industrial practical examples for better understanding and learning. if you have not yet read these free template articles/posts then, you could visit our “Template/Format” section. Thanks for reading…keep visiting techiequality.com
Useful Post:
3MU Check sheet | Details of MURA, MURI & MUDA|Download
4M Checklist Template |Free Download Format
How to enhance production in manufacturing unit?
Fault tree analysis template | Download format free…
More on TECHIEQUALITY