Equipment Ranking Process | A B C Ranking of Machine with Manufacturing Example
Equipment Ranking Process | A B C Ranking of Machine with Manufacturing Example:
Hi readers! Today we are going to discuss on equipment ranking process, it is an important part of the maintenance process, where machines/equipment/ parts will be ranked and based on the rank category, and you can easily set up the maintenance principle. The organization will get benefits in terms of productivity, quality, cost, safety, etc., and also it will help you to select the type of maintenance applicable / applied on which machine.
Equipment Ranking Process:
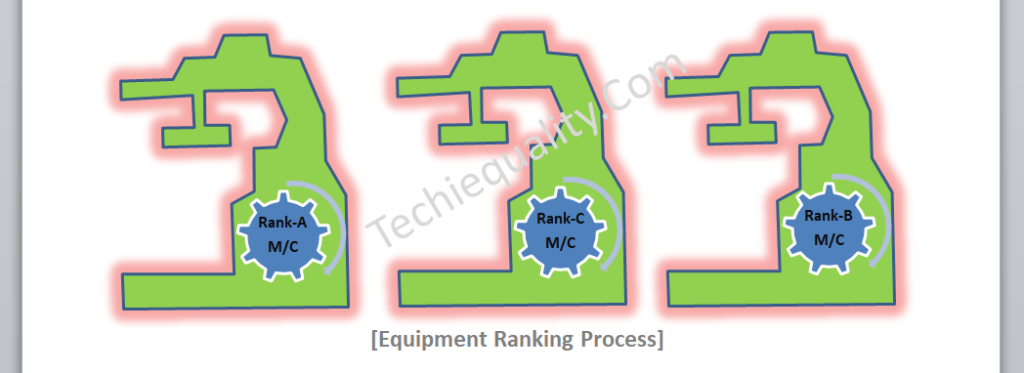
If first time, you are going to implement it in your organization then you have to formalize many more things like SOP, Check-sheet, list of equipment/ machine, machine /equipment ranking criteria, data, etc. so here, we will help you for easy implementation of this process.
Step by step process has been defined below to implement the machine /equipment ranking process in your manufacturing organization;
Step-1: Prepare the SOP, List of equipment, and equipment/machine ranking criteria procedure.
In the ranking criteria, you can consider the PQCDS means Production, Quality, Cost, delivery, and safety as weightage for factors in categorization, but some industry also considers other factors like Maintenance / Maintainability, Operability, etc.
All the above factors are not equally important and they vary from industry to industry based on the application, material used, quality, safety, etc. For example, equipment is being used for chemical handling, safety factors get a high weightage for rating calculation. And similarly, imported machines may come under high weightage on maintainability if spare parts are mostly imported procurement may take more time and the cost of repair could be high.
Step-2: Form a CF-Team, including Production, quality, maintenance, and safety personnel for best weightage consideration.
For example, let’s say we are having total of 16 machines, and according to their criticality w.r.t PQCDSM and consultation with CF-Team, finally, we have broadly done the weightage of factors of individual machines or similar types of machines.
Machine-1
P-Production | 100 |
Q-Quality | 100 |
C-Cost | 50 |
D-Delivery | 50 |
S-Safety | 20 |
M-Maintainability | 20 |
Total = | 340 |
Machine-2
P-Production | 100 |
Q-Quality | 90 |
C-Cost | 50 |
D-Delivery | 40 |
S-Safety | 40 |
M-Maintainability | 40 |
Total = | 360 |
Machine-16
Production-P | 100 |
Quality-Q | 80 |
Cost-C | 50 |
Delivery-D | 40 |
Safety-S | 40 |
Maintainability-M | 40 |
Total = | 350 |
Similarly, you can do the weightage of factors of all machines or you can prepare the common criteria sheet for similar types of Machines.
Step-3: Prepare the final ranking criteria sheet.
For example, we have prepared the below-ranking criteria sheet for reference only, you can prepare according to your organization’s decision and machine’s factors, operations, etc. but here we have made the generic criteria rules is given below.
Let’s say “Quality” factors have 100 marks and we have divided them into four degrees of factors.
Mark=100 | 80 | 60 | 40 |
Always being required to work to a very fine tolerance or Equipment failure mode has a major effect on quality, the product produced out of Specification. | Produce quality variations, some of the products may get rejected but the operator’s intervention requires less time to correct it. | The Product can be reworked and used, meets the specification and drawing, machine is sufficiently accurate for required tolerance. | No quality problems, no effect on quality, and no product defects. |
Accordingly, you can prepare the ranking criteria matrix for Production, cost, safety, delivery, and maintainability, etc.
Let’s consider the machine-1, factors given in above i.e.
P-Production | 100 |
Q-Quality | 100 |
C-Cost | 50 |
D-Delivery | 50 |
S-Safety | 20 |
M-Maintainability | 20 |
Total = | 340 |
The total mark of the entire above factor (PQCDSM) is 340. Based on the organization’s decision and degree of factors mark, an organization can decide the range for the category of machine, e.g.
Up to 130 marks ——-C Rank / Category
131 to 190 marks ——-B Rank / Category
191 to 340 marks ——- A Rank / Category
As you know that we have considered 16 machines, so our CF-team members have collected and gathered the machine history records, data and with the help of the ranking criteria matrix, they have evaluated the entire machine, and the same is mentioned below the table.
Machine | Rank / Category |
M/C-1 | A |
M/C-2 | B |
Machine-3 | C |
M/C-4 | C |
M/C-5 | A |
Machine-6 | B |
M/C-7 | A |
Machine-8 | B |
M/C-9 | B |
Machine-10 | B |
M/C-11 | A |
Machine-12 | B |
M/C-13 | B |
Machine-14 | A |
M/C-15 | C |
Machine-16 | C |
According to the machine’s rank, you have to prepare the maintenance plan, e.g. our maintenance engineer has decided that M/C-1 will be covered under preventive and predictive maintenance twice a month and similarly M/C-8 will be covered under preventive maintenance twice a month. And M/C-16 may be covered under preventive maintenance once a month or only BM. So, in this way, you can prioritize the machine maintenance period w.r.t m/c or equipment category or ranking.
Free Templates / Formats of QM: we have published some free templates or formats related to Quality Management with manufacturing / industrial practical examples for better understanding and learning. if you have not yet read these free template articles/posts then, you could visit our “Template/Format” section. Thanks for reading…keep visiting techiequality.com
Useful Post:
What is Preventive Maintenance? | Predictive Maintenance |Types & Example
Plan Do Check Act Cycle | PDCA Cycle Manufacturing Example | Implementation
Attribute MSA |How to do Attribute type MSA Study| Example |Acceptance Criteria
Gage R and R |Attribute type MSA |How to do MSA Study | Acceptance Criteria
More on TECHIEQUALITY